Have you ever wondered what it would be like to do the same exhibition again? Do the opportunities for avoiding mistakes make it different or better? Well, that’s kind of the situation we ran into recently.
How it all began
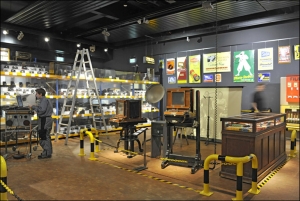
TECHNOSEUM, picture Klaus Luginsland
In 2010 the museum building needed to take clearing-up measures that ate up much of the budget. But, of course, our visitors still wanted to see something. No money, no staff, no time – was there a solution? Yes, there was. We still had our own collections! Minimum transportation costs, no courier fees, no insurance problems. If we used only storage racks as showcases and archival materials for presentation we didn’t need much exhibition design and could re-use the materials afterwards. The more we thought about it, the more we fell for the idea. As an extra, we could check a large amount of our collection, correct data base entries, maybe retrieve some of the “location unknown“ artifacts and resolve some “found in collections.” To make a long story short, in 2011 we opened “Die Sammlung: 1001 Objekt zum Hören und Sehen“ (The Collection: 1001 Artifacts to Listen To and Look At), a presentation of our collections of radios, TV sets, record players, film projectors, cameras, tape recorders, video recorders… Our visitors loved it!
So, as you can imagine, when it became clear we would repeat the exhibition using our collection of household appliances, we were all excited. And while team spirit during the preparation of the first collection’s exhibition was like manning an expedition ship and sailing into the Great Unknown, this time it was like a soccer match against our former selves: we wanted to make it bigger, better and more colorful than the first time.
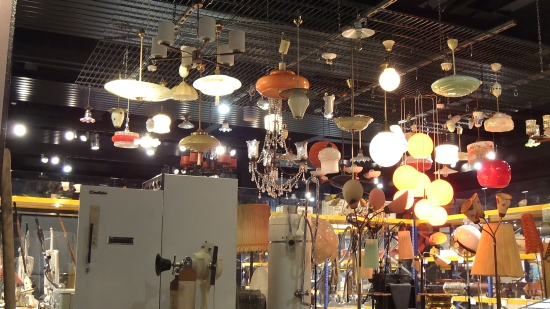
Picture: Bernd Kießling
Spirit of improvement: Right or left – my position
We knew what worked well last time and so we had a map to follow. But instead of following it slavishly in the spirit of “we always did it that way,“ we followed it in the spirit of improvement.
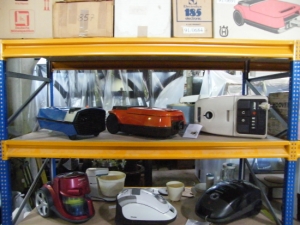
For example, the first time we had tested all layouts of the artifacts on the shelves beforehand. We had a rack similar to those in the exhibition set up in the storage area, so we could arrange the artifacts until they looked best. Investing in the time to do this during preparation reduces stress during the final installation process. In addition, it’s not important who does the final installation. The positions on the racks are clear, so anybody with experience in artifact handling can do it without taking time thinking about the perfect layout.
After the artifacts were arranged we gave them position numbers on the shelf. The first time we went with directions, so our packing lists looked like this:
Inventory number, object name, rack number, shelf number, left
While this had worked pretty well, we made some observations:
- Positioning with terms like left and right might seem clear on paper, but if you have team members who sometimes confuse left and right (like myself), mistakes in positioning are likely to happen.
- Left, middle and right work well if you only have three radios on the shelf. You can work with more artifacts by inventing terms like “outer left“ and “middle left.” This sounds charming, but impractical.
So we switched to using position numbers from 1 on up, numbering from left to right. Now our packing lists looked like this:
Inventory number, object name, rack number, shelf number, Pos. (for position number) 3
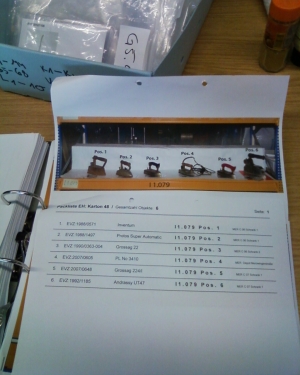
For the same reason we decided to take an additional step in preparation. The first time we had noted the positions on the shelf only in our data base. This time we took a picture of every shelf layout and wrote the position numbers on it. We attached the picture to every packing list. Now, whoever was positioning the artifacts during installation could use the picture as a reference.
This was only one example of the many things we improved during preparation.
A second loop of improvement
We all worked in “improvement mode“ during preparation and continued that way during installation. We ran into several things we could do better next time.
For example, after we attached the exhibit labels, we took down the inventory cards and collected them. The first time we had collected them all in a box and sorted them by inventory number so that they could be found pretty quickly once one had the inventory number.
Suddenly our student assistant said, “Wait a minute, wouldn’t it be better to collect and store them by rack and shelf number?“
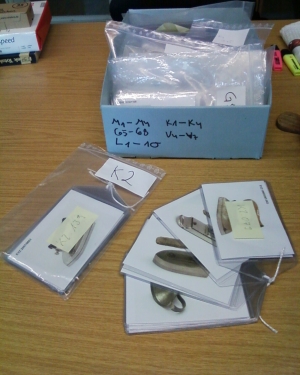
We briefly discussed the idea, approved it, and in his honor named it “The Pakenis Maneuver.” From this moment on we collected the inventory cards in zip-lock bags, one for each shelf, with the rack number and shelf number written on them. When we take down the exhibition everybody can grab the bags of the rack she or he has to pack up and is equipped with the appropriate inventory cards.
Another example is the layout pictures. I described how we prepared them and it sounded pretty good to you, didn’t it? Yep, thought so. We were pretty proud of the idea. However, during preparation we realized that it was a good idea, but not the best.
We had a picture attached to every packing list, which wasn’t necessary. Most of the time we simply took the picture from the first box, put it on the shelf and used this picture as a reference. So, in the future we can skip the effort of printing out the picture and attaching it to the packing list. We will print all the pictures immediately before preparation and place them on the corresponding shelves. This will save some paper and ink, too.
Having the position numbers written on the pictures was of help but you had to skip between the picture and the packing list, because you had the inventory number on the artifact and the packing list, but not on the picture. This also led to confusion with similar-looking artifacts on the same shelf. Next time we will also write the inventory numbers on the picture.
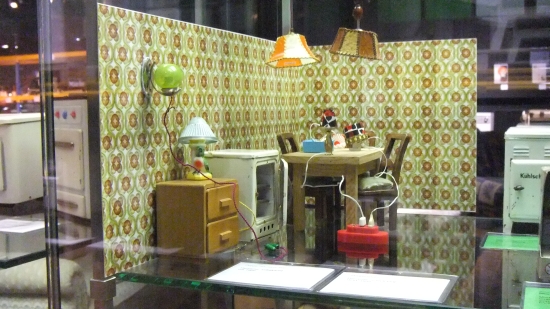
The art of making mistakes
One thing we realized during preparation and installation was that we ran into mistakes we had already made the first time. Not wanting to admit mistakes is human. Making the same mistake twice is dumb. The main mistake we made last time was not making notes of what didn’t work. So we only improved the things we remembered, while we were forced to repeat the mistakes we forgot.
Being in “improvement mode“ we decided to do it better this time. Every time we realized something that could have been improved upon, someone said, “Stop. Make a note!“ And we did. It didn’t matter if we were standing on ladders, cleaning acrylic glass or attaching labels; someone always took a quick note of what we had realized.
Shortly after the exhibit opening we sat down, collected all our notes and discussed other things we remembered. We will collect them all in one paper, including the things that worked well and that we will definitely do again. This might serve as a reference for upcoming collections exhibitions and even if many of our suggestions are very specific, some might be helpful for other projects, too.
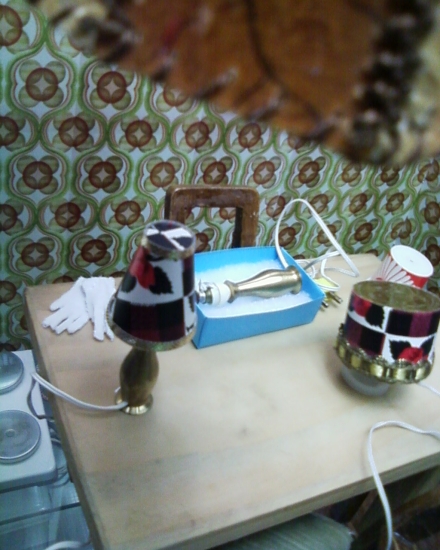
Our Score
On February 19 we opened “The Collection 2: The Electrical Household.”
If you have 3D glasses (red-cyan) you can follow our 3D virtual tour. If you haven’t, you may visit our picture gallery.
You may take a look at those two videos from German TV:
http://www.rnf.de/mediathek/kategorie/themenserien/technoseum-mannheim/#.UwoZBYUnYyM
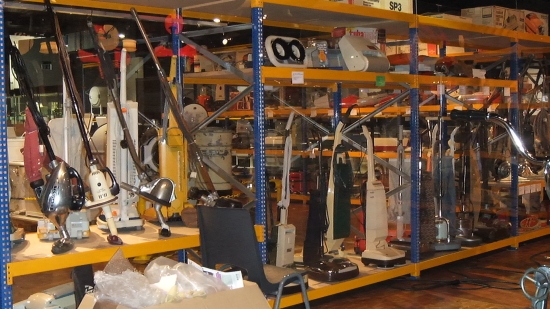
Picture: Bernd Kießling
I said we were like a soccer team playing against our former selves. So, what was the score?
- We showed more artifacts than the first time (1750 against 1639, but the first figure included about 300 archival items, while this exhibition was composed almost entirely of artifacts).
- We had a closer collaboration with our marketing department, resulting in more blog entries, a Christmas tree decorated with household appliances and a Tweetup (#Sammlung2).
- We looked into a greater number of artifact groups and therefore were able to set more data base entries straight.
- Both times, we were done with the basic installation a few days before opening, allowing us to improve some more things immediately.
- Let’s see if we can improve on the number of visitors to the first exhibition, which was 14,400 higher than expected.
But there’s no reason to stop here. When it comes to doing things better, there is no finish line. Next time our rallying cry will be again:
Go, get us!
P.S. During preparation we learned many things (such as: why check shelves before screwing acrylic glass to the front) so there is material for a few more stories on Registrar Trek. Stay tuned!
Like always brought from German English into correct English by Molly Hope.